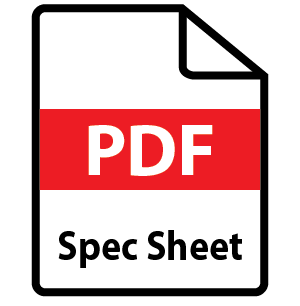
Single Piece Casting: Meehanite®
The 400S & 400SY are built from an 8,300 lb single piece casting with the table at a 45° slant. The casting has been designed with many access ports to improve the serviceability of the machine. The chip and coolant flow are directed to the front of the machine for convenient installation of a chip conveyor on the side. We are providing large X & Z servo axis motors with this system, and the rigidly of the machine can accommodate extremely aggressive machining applications. These models are the real Industrial Strength Gang Tool & Turret Designed Machine Tool Systems that will meet the needs of customers in today’s competitive market.
Cross Slide: Linear Bearings Provide for Low Friction Feed
The 400S & 400SY cross slide design incorporates a high-performance positioning system featuring high preload, low friction, four circuit, roller linear bearings manufactured by Swedish manufacture SKF, and a precision-ground ball screws manufactured by Taiwan manufactures PMI/Hiwin. Machine is available with optional roller bearings on request. The performance slide utilizes state-of-the-art AC brushless servomotors and digital drives. Linear guides are 30mm sets and are extremely rigid, and the ball-screws are precision ground, 32mm, 08 mm-Lead in a. Both the linear rail bearing blocks and ball screws are outfitted with brass lines and fittings with a timed lubrication system.
Spindle Options: Wide Range of Work Holding Options Available
The 400S & 400SY standard spindle option is a 45 mm diameter spindle with a 4,500-maximum rpm. The main spindle is an A2-6 mount and the counter spindle are A2-5 mount. We offer a wide selection of work holding from ATS Systems. This spindle has a hydraulic collet closer.
C-Axis Spindle: Mill and Turn Difficult Parts Efficiently
The 400S & 400SY spindle design allows for the flexibility and capability to do parts that normally require machinery that costs significantly more. The C-Axis Spindle allows you to mill and turn parts off center. Slots, cross-holes, bolt-hole circles, ID keyway broaching, and radial and axial milling, with many other secondary processes traditionally requiring a milling machine/machining center, can be performed on the gang lathes in combination with turning operations. The C-Axis spindle achieves performance in the most complex duty cycles and allows for the use of live tools.
400S & 400SY
|
Capacities
|
S.A.E
|
Metric
|
Max Swing Over Bed
|
22.8 in
|
580 mm
|
Max Swing Over Carriage
|
13.7 in
|
350 mm
|
Max Turning Diameter
|
9.8 in
|
250 mm (with specific turret)
|
Max Between Chucks
|
19.6 in
|
500 mm
|
Max Turning Length
|
16.9 in
|
430 mm
|
Main Spindle
|
|
|
Spindle Nose
|
A2-6
|
A2-6
|
Spindle Chuck
|
8”
|
203 mm
|
Spindle bore
|
2.4 in
|
61 mm
|
Bar Capacity
|
1.96 in
|
49 mm
|
Spindle Speed (Max)
|
4500 rpm
|
4500 rpm
|
Collet Actuator
|
Hydraulic Cylinder
|
|
Counter Spindle
|
|
|
Spindle Nose
|
A2-5
|
A2-5
|
Spindle Chuck
|
6”
|
152.4 mm
|
Spindle Bore
|
2.2 in
|
56 mm
|
Bar Capacity
|
1.7 in
|
44 mm
|
Max RPM (Max)
|
4500 rpm
|
4500 rpm
|
Travels & Feedrates
|
|
|
X-Axis Travel
|
9.0 in
|
230 mm
|
Z-Axis Travel
|
20.8 in
|
530 mm
|
Z2 (Sub Spindle) Travel
|
20.8 in
|
530
|
Y-Axis Travel
|
4.7 in
|
120 mm
|
Rapid on X-Axis
|
945 in/min
|
24 m/min
|
Rapid on Z-Axis
|
945 in/min
|
24 m/min
|
Axis Max Feed Rate
|
400 in/min
|
10.15 m/min
|
Motor Power
|
|
|
Main Spindle Motor
|
10 HP
|
7.5 kW
|
Counter Spindle
|
7.5 HP
|
5.5 kW
|
X/Z Axis Motors
|
1.5/2.3 kW
|
2/3.1 HP
|
Coolant Pump
|
0.7 HP
|
0.49 kW
|
Hydraulic Station Motor
|
1.5 HP
|
1 kW
|
Tool Change System
|
|
|
Turret Type
|
Hydraulic/Servo Driven
|
Hydraulic/Servo Driven
|
Turret Model
|
LS-200DBR 12 Station
|
12-Station Servo Driven Live Tools
|
Tool Holder Type
|
DIN69880 & DIN5480
|
DIN69880 & DIN5480 Standards
|
Center Height
|
100 mm
|
100 mm
|
Hydraulic Cylinder
|
Clamping Force
|
4,240 kg.
|
Base
|
|
|
Integral Casting
|
One Piece Construction
|
Slant Angle 45 Degree
|
Rail Span
|
15.7 in
|
400 mm
|
Linear Rails
|
X/Z 1.81 in P Accuracy
|
X/Z 30mm P Accuracy
|
Ball Screws Precision
|
X/Z Ground 1.26 in C3 Accuracy
|
X/Z Ground 3208 mm C3 Accuracy
|
Timed Auto Lubrication
|
Linear Rails &
|
Ball Screws
|
Head Stock
|
Cast Iron
|
Cast Iron
|
Precision
|
|
|
Positional Repeatability
|
±0.0001 (one tenth)
|
0.00254 mm
|
Positional Resolution
|
±0.00005(50 millionths)
|
0.00127 mm
|
Positional Accuracy
|
±0.0001 (one tenth)
|
0.00254 mm
|
Spindle Runout
|
0.00005 (50 millionths)
|
0.00127 mm
|
C-Axis Indexing
|
Increment 0.001°
|
360,000 Radial Position
|
Requirements
|
|
|
Coolant Capacity
|
18.5 gallons
|
70 Liters
|
Power Required
|
30 KVA
|
Voltage 208-240 VAC 3-Phase
|
Machine Dimension
|
|
|
Machine Height
|
72 in
|
1830 mm
|
Sheet Metal Length
|
120 in
|
3050 mm
|
Sheet Metal Width
|
70 in
|
1750 mm
|
Machine Weight
|
8300 lbs
|
3765 kgs
|
GSK 988TD CNC Control
GSK is the second largest producer of CNC kits annually producing approximately 500 CNC systems per week. On over 25 billon dollars worth of machine tools produced in China annually over 65% have GSK CNC components. This is not a PC-based system, but a hardened CNC with the software burnt into the eproms of the hardware providing maximum reliability. The modular design of the products allows quick replacement of major components if and or when required. GSK provides complete CNC systems which includes all required motors, drives, cables, and controls. The NEW 988TD CNC control is a dual-channel turning center CNC control developed by GSK Equipment Co., LTD. It is based on ARM+DSP dual-core hardware architecture by connecting with the industrial Ethernet bus with the (GSK-Link), the servo drives and a remote I/O unit. The 988TD can control up o 10 axis and 4 spindles, each path includes 6 feed axis (including C Axis) in each path, 3-axis link and 3 spindles to realize the turning with compound milling operations. The servos motors use high-resolution absolute encoders that provide 0.1µm position precision, and 1ms interpolation period to perform a turning-milling compound machining and can provide the control performance for multi-axis turning and machining centers.
429-2060
X & Z Motors & Drives option
|
X & Z axis servomotors and drives used with the GT-5 lathe model. X-Axis motor has a built-in brake.
|
GSK Axis Package: Servomotor & drive: (1.5 KW, 1,500 Watts, 2 hp, Stall torque 6.2 Nm, Maximum thrust X-Axis is 1411 lbs. and 6,280 newton and maximum thrust Z-Axis 847 lbs. and 3,768 newton 2,500 rpm, 6A, 5000 ppr encoder, 130 mm flange.
|
Spindle Motor & Drive Option
|
7.5 hp C-Axis spindle motor & drive package. Optional
|
AC servomotor and drive (7.5 hp, 5.5 Kw, 5,500 Watts, max speed 7,000 rpm, and 4096 encoder. Maximum torque 46 ft/lb or 63 Nm.
|
Technical Characteristics
- 10 Feed axis (including C-Axis), 4 spindles each path includes feed axis (including C-Axis) in each path, 3-Axis link and 3-Spindle to realize the turning and milling compound machining.
- Command unit 1µm, and 0.1µm, 1µm up to 240 m/min. 0.1µm up to 100 m/min
- The servo drive and I/O unit use connection control of the GSKLink bus
- Nested many PLC programs, PLC ladder on-line editing
- Part programs edited in the background
- Network interface, remote monitoring and file transmission
- USB interface, U disc file operation, system allocation and software upgrading
Technical Specifications
- Controllable Axis
- 10 feed axis (including C-Axis), 4 spindles; each path includes 6 feed axis in each path, 3-axis link and 3 spindles to realize compound turning and milling functions.
- PLC controllable axis number 10, 6 axis in each path
- Axis Feed Functions
- Least Command Unit: 0.001 mm and 0.0001 mm
- Least Command Range: ±99999999 X least command unit
- Rapid Traverse Speed: max: 240 m/min in 0.001 mm command unit, max 100 m/min in 0.0001 mm command unit.
- Rapid Override: F0, 25%, 50%, 100% real-time tuning
- Cutting Feedrate: 0.01 mm/min ~100000 or 0.01 inch/min ∼ 4000 inch/min (G98: feed per minute) 0.001 mm/rev ~ 500 mm/rev or 0.0001 inch/rev ~ 9.99 inch/rev (G99: feed per rev)
- Feedrate Override: 0 ~ 150% 16-level real-time tuning
- Interpolation mode: linear, circular, thread, polar, cylindrical interpolation and rigid tapping
- Thread Function
- Thread Type: constant pitch straight thread/taper thread/end thread, variable pitch straight thread/taper thread/end thread
- Thread Pitch: 0.01 ~ 500 mm (metric thread) or 0.0001 inch ~ 9.99 inch (inch thread)
- Thread Run-Out: thread length, angle speed can be set
- Acceleration/Deceleration Function
- Cutting Feed: Linear pre-acceleration/deceleration
- Rapid Traverse: S-Type
- Initial Speed: terminal speed and time acceleration/deceleration are set by the parameters
- Spindle Function
- 3-channel spindle control in each path, 4-spindles, multi-spindle control
- Spindle Speed: spindle speed specific by S or PLC signal range 0 rpm ~ 20000 rpm
- Spindle Override: 50% ~120% 8-level real-time tuning
- Spindle constant surface control
- Rigid tapping
- Tool Function
- Tool length compensation (tool offset): 99 groups
- Tool Wear Compensation: 99 groups of tool wear compensation data
- Tool Nose Radius Compensation: C-Type
- Tool Setting Mode: fixed point tool setting, trial cutting tool setting, reference position return tool setting
- Precision Compensation
- Backlash Compensation: compensation range (-9999 ~ 9999) x check unit
- Memory Pitch Error Compensation: 1024 compensation points, compensation point number of each is set by parameter, each point compensation range (-700 ∼ 700) X check unit
- PLC Function
- 13 Basic Commands, 50 functional commands
- PLC ladder on-line edit, real-time monitoring
- 2-level PLC program up to 12000 steps the first level program refresh period 8 ms
- PLC Programs (up to 16) the current running PLC program can be selected
- I/O Unit
- Rapid I/O: 16 input/ 8 output
- Operation Panel I/O: 118 input/ 96 output interface
- Up to 4 GSKLink remote I/O Interfaces: each i/o has 72 input interfaces and 48 output
- Human-Computer Interface
- Display in English, Spanish, Russian and Chinese
- Two-dimensional tool path and solid graphic display
- Servo State Monitoring
- Servo parameter on-line allocation
- Real-time Clock
- On-line help
- Operation Management
- Operation Mode: Auto, Manual, Edit, MDI, DNC, MPG and reference position return
- Multi-level operation authorization management
- Alarm log
- Timed stop
- Program Edit
- Program Capacity: 25M, 10000 programs (including subprogram and macro program)
- Edit Mode: full screen edit part program edit on the background
- Edit Function: searching, modifying and deleting programs/blocks/words, coping and deleting blocks
- Program Format: ISO code (A set of G code, B system of G code) word without blank space, relative coordinates, absolute coordinate compound programming
- Program Call: macro program call with parameters, 12-level subprogram nesting
- Aided Programming: common used cycle commands using graphic aided programming
- Grammar Check: executing the rapid grammar check for the program (do not run the program) after it has been edited
- Path Preview: do not run programs, use the path preview function to check the program path
-
- Communication Functions
- USB: U disc file operations, U disc file directly machining, upgrading PLC program and system software u disc
- LAN: remote monitoring, network DNC machining, file transmission remotely upgrading PLC program, and system software, CAD/CAM
- Safety Functions
- Emergency stop
- Hardware travel limit
- Many storage travel checks
- Data backup and recover
400S & 400SY 12-Station Power Tool Turret:
The 400S & 400SY tuning centers have a LS-200DBR 12-Station Servo Turret manufactured by Lio Shing one of the largest manufactures of turrets in Taiwan with a gear ratio of 1/30, Hydraulic power source: P=40 kg/CM2, and clamping force of 4,240. Design includes three-piece type curvic clutch ensures high precision accuracy. Tool holders are driven by a servomotor that features high torque output and with low noise. Repeatability accuracy reaches 0.003 mm. 4,000 maximum high speed. Inside mechanism employs parallel cam, featuring high indexing accuracy and fast tool change. Turret clamping/ unclamping is operated through hydraulic power, assuring smooth motion and permitting for heavy duty machining. The turret can be mounted at right or left side with random tool selection function. Tool Shank Specifications: VDI40, DIN69880, DIN5480 W20 X 0.8/ BMT65-ER32
LS-200DBR
|
1
|
Turret rotation and indexing is driver by servomotor and drive. Tool Holders are drive by servomotors with high torque and no noise design. Power tool meet DIN69880 and DIN5480 standards. Hydraulic cylinder clamping force is 4,240 kg.
|
Rotation
|
|
Servo Motor
|
Center Height
|
MM
|
100
|
Number of Tools
|
N
|
12-Station
|
Rotating Time (tool-to-tool)
|
Sec
|
0.47 Seconds
|
Rotating Tool (including locking)
|
Sec
|
0.57 Seconds
|
Total Indexing Time
|
Sec
|
180 Degrees 1.4 Seconds
|
Total Indexing Time
|
Sec
|
180 Degrees including locking 1.5 Seconds
|
Curvic Coupling Type
|
|
3-Piece Design
|
Tool to Motor Transmission
|
|
Gear Ratio 1-1
|
Turret Servo Motor
|
|
Options, GSK, Fanuc, Mitsubishi
|
Hydraulic Working Pressure
|
Kg
|
40 kgf/cm
|
Flow Rate
|
|
L/min. 30
|
Thrusting Force of Hydraulic Cylinder
|
Kgf
|
4,240
|
Accuracy of Repeatability
|
SEC
|
±0.003 mm
|
Net Weight (No Motor)
|
Kg
|
245 kg
|